Executive Summary
TaylorMade Golf (TMG), a pioneer in golf equipment manufacturing, constantly endeavors to innovate and redefine standards in the sports equipment sector. In a collaborative partnership lasting five years, AlphaBOLD has empowered TaylorMade Golf to navigate through diverse business challenges and implement transformative projects. Beyond the successful implementation of Dynamics 365 for business efficiency, AlphaBOLD led the Bullseye 2.0 project, to refine the golf club bending machine’s software capabilities. This innovative integration solution pioneered a new degree of automation in bend operations, resolving challenges in authentication, supervisor interventions, automatic bend requirement loading, and data synchronization with the Manufacturing Execution System (MES).
Bottlenecks TMG Previously Countered
The amalgamation of industrial machinery introduced substantial challenges, intensified by the use of a specialized technology stack developed in Microsoft Foundation Class Library (MFC). The existing system at TaylorMade grappled with:
- Dependence on Preliminary Setup Data: The lack of regular synchronization with the MES (and its off-line mode use) resulted in inconsistencies and outdated data, affecting club bending operations.
- Human Error Risks: The necessity for manual inputs and parameter adjustments in offline mode jeopardized accuracy and operational efficiency in the following ways:
- Incorrect bend angles or measurements, impacting club performance.
- Manual input errors causing delays, requiring backtracking or assistance.
- Reduced operational efficiency and cost overruns.
- Delayed Real-time Updates: Alterations made to work orders, club details, or bending parameters were not immediately updated, impacting transparency and overall process management.
Partner Solution: Impact of Integration with MES
TaylorMade faced challenges while managing the manual configuration and setup of the application, resulting in errors or inconsistencies in club bending operations. AlphaBOLD’s experts conducted a comprehensive analysis and evaluation of the current solution to develop a customized approach that successfully addresses functional, operational, and business-related concerns at TaylorMade.
The specialized intervention provided a user-friendly toggle feature, enabling users to switch between offline and online modes effortlessly. In the offline mode, the machine employed a traditional club bending method, where the bend parameters were manually set. On the other hand, the online mode seamlessly integrated the system with a MES, resulting in a revolutionary experience for operators. This has allowed the TMG team to benefit from:
- Seamless Integration with MES: The integration with MES enables real-time access to accurate and current data, streamlined authentication, and work order retrieval, improving operational fluidity and data accuracy. Authentication and work order retrieval: MES authentication system enables operators to authenticate themselves by scanning their badges, saving time and effort. Additionally, users can scan a work order to fetch relevant club information from MES, eliminating the need for manual data entry.
- Automated bending requirement setup: In the online mode solution, operators now scan the club’s head Q.R. code, automatically setting the machine’s bending parameters. This automation significantly eliminated human error probability and ensured consistent and accurate bend settings.
- Enhanced Workflow Management: Through seamless integration with MES, which provides operators with a transparent view of work orders and their associated clubs, tasks can be effectively prioritized and managed. This results in reduced delays and optimized productivity.
- Multilingual Support: Apart from English, the solution supports Spanish, Japanese, and Korean languages. This enables operators across various countries, including Mexico, Japan, Korea, the US, and Australia to utilize the solution effectively in their local languages.
Experience advanced automation and seamless system integration with AlphaBOLD
Request a ConsultationEnhanced User Experience & Business Efficiency
AlphaBOLD’s technical proficiency has introduced an elevated level of automation and integration, improving interactions between users and the systems.
The sophisticated data generated by the Bullseye V2.0 solution is a valuable source of insights for managers, and operators alike. It has enabled them to identify trends, patterns, and potential bottlenecks in the bending process, facilitating proactive decision-making and continuous optimization.
By combining error-proofing measures, enhanced automation, and seamless integration, AlphaBOLD’s contributions directly impacted business efficiency. Moreover, it has lowered operating overhead, reduced material write-off risk, and ultimately elevated customer satisfaction.
Conclusion
AlphaBOLD’s pivotal role in refining TaylorMade Golf’s processes has set new standards in automation and precision within the industry. The integrative solutions provided have eliminated operational bottlenecks, optimized employee and system efficiency, and introduced groundbreaking innovations in sports equipment manufacturing and servicing, reinforcing TaylorMade’s commitment to continual innovation and excellence.
Experience advanced automation and seamless system integration with AlphaBOLD
Request a ConsultationExplore Recent Case Studies
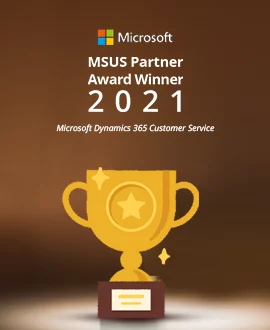